Ремонт и модернизация автомобильных деталей для повышения их надёжности
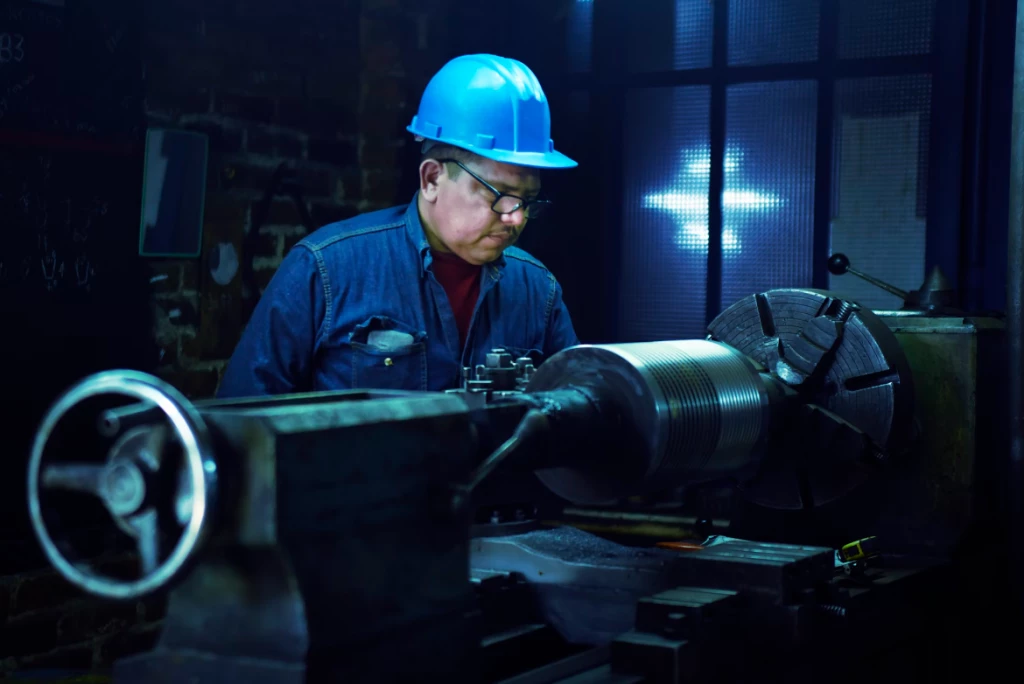
Автомобильные детали — это важные составляющие любого транспортного средства, от которых зависит его надежность, производительность и безопасность. При эксплуатации автомобиля детали могут изнашиваться, выходить из строя или требовать модернизации для улучшения их характеристик. В таких случаях ремонт и модернизация автомобильных деталей становятся необходимыми процессами для обеспечения надежности и долговечности автомобиля.
Надежность — это сложное понятие, которое варьируется в зависимости от назначения и условий эксплуатации изделия. Такие факторы, как надежность, долговечность, безопасность и ремонтопригодность, являются важными факторами. Ведущие мировые производители автомобилей используют системы автоматизированного проектирования (CAD), например, четвертого поколения (CAD/CAM/CAE/EDMS), для проектирования и производства своих автомобилей.
Например, одна автомобильная компания использует высококачественное программное обеспечение Pro/ENGINEER для проектирования своих продуктов. Проектирование с использованием этих систем начинается с создания трехмерной твердотельной модели продукта. Затем инженеры определяют основные механические свойства материала и анализируют смоделированные упругие и пластические деформации, вызванные внешними воздействиями на исследуемый объект. Кроме того, такие инструменты, как Pro/MECHANICA, позволяют инженерам моделировать статические, кинематические и динамические процессы для оптимизации геометрии и конструкции компонентов.
Модули для сборки крупных компонентов предоставляют широкие возможности управления сложными сборками с учетом допусков и подгонки, которые являются важными аспектами производства автомобилей. Однако из-за различных технологических факторов и ошибок фактический профиль поверхности детали всегда отличается от заданного на чертеже или смоделированного с помощью систем автоматизированного проектирования (CAD). В результате режимы резания и последовательности обработки с ЧПУ, разработанные для идеализированной математической модели объекта, могут не обеспечивать желаемого уровня точности при обработке реальной детали.
Для решения этой проблемы мы предлагаем внедрить контроль геометрической точности автомобильных компонентов на различных этапах производственного процесса с использованием специализированного измерительного оборудования. Фактические геометрические данные, полученные в результате этих измерений, затем могут быть автоматически переданы в систему автоматизированного проектирования (CAD) через специальный модуль, позволяющий вносить коррективы в процесс проектирования в режиме реального времени.
Использование CAD-систем при восстановлении деталей и узлов автомобиля может быть сложной задачей, поскольку часто возможно лишь частично использовать некоторые CAD-модули из-за сложных технологических процессов, связанных с восстановлением. Эти процессы трудно смоделировать математически, поскольку они по своей сути являются вероятностными, что затрудняет точное прогнозирование результатов.
Однако, несмотря на эти трудности, восстановление деталей машин обеспечивает значительную экономию высококачественных металлических материалов и рабочей силы. Как вы, наверное, знаете, восстановление изношенных деталей автомобилей требует меньшего количества технологических операций, чем изготовление новых деталей. Это особенно актуально сегодня, когда более половины всех продаваемых автозапчастей являются восстановленными. Однако срок службы восстановленных деталей зачастую короче, чем у новых, из-за сокращения объемов производства по ремонту автомобилей за последние 15 лет и соответствующего снижения качества восстановления автомобильных деталей.
Тем не менее, существует множество современных и инновационных методов восстановления автомобильных деталей, которые не только возвращают им первоначальные размеры и форму, но и продлевают срок их службы по сравнению с новыми. Некоторые из этих методов включают:
наплавка (высокоскоростная электродуговая наплавка в среде защитного газа с добавлением металлического порошка; высокоскоростная плазменная порошковая наплавка прямой дугой; плазменная; вибродуговая; дуга под флюсом; индукционная и т.д.);
методы газотермического напыления (пламенное, плазменное, электродуговое, детонационное, и высокоскоростной), а также холодное газодинамическое напыление;
сварка электродами, проволокой, аргоном и CO2, а также процесс "холодной сварки" различными металлическими и полимерными композициями;
электроконтактная и индукционная выпечка порошков, а также нанесение гальванических ремонтных покрытий;
пластическая деформация, термическое упрочнение и другие виды обработки поверхности;
неабразивная ультразвуковая чистовая обработка, магнитное истирание и ультразвуковая абразивная обработка.
Примерно 70% работ, связанных с ремонтом деталей, включают наплавку и сварку. Выбор метода зависит от таких факторов, как материал детали, степень и тип повреждения, толщина, технические требования, экономические показатели и другие факторы. В любом случае, при ремонте деталей важно обеспечить требуемую шероховатость поверхности, точность размеров и взаимное расположение поверхностей. Кроме того, необходимо учитывать твердость, непрерывность покрытия и прочность сцепления нанесенных слоев с основным материалом.
Широкому внедрению этих методов для восстановления автомобильных деталей препятствовала сложность обработки обработанных поверхностей, что часто приводило к отсутствию желаемого качества поверхности. Это особенно актуально для поверхностей, которые были отремонтированы с помощью наплавки или нанесения износостойких порошковых покрытий. Эти покрытия состоят из твердых частиц карбида, внедренных в более мягкую металлическую подложку, что затрудняет их обработку обычными методами.
В дополнение к электрофизическим и электрохимическим методам, эффективным подходом является шлифовка этих поверхностей с использованием абразивных инструментов. Для обработки хромированных поверхностей чаще всего используется круговое шлифование. Однако несоблюдение предписанных условий и техники шлифования может привести к отслаиванию покрытия или образованию трещин и следов ожогов. Кроме того, абразивные круги могут засаливаться, что, в свою очередь, не может не сказаться на качестве обрабатываемой поверхности. Как уже упоминалось ранее, состояние поверхностных слоев деталей во многом определяет долговечность и надежность технического оборудования.
Одним из возможных решений этой проблемы является использование ленточного глубокого шлифования для обработки наплавленных поверхностей. Этот инновационный вид обработки обладает рядом преимуществ по сравнению с традиционным шлифованием абразивным кругом как с точки зрения глубокого шлифования, так и с точки зрения многопроходных операций.
Особенностью шлифования абразивными лентами является то, что оно создает остаточные напряжения сжатия в поверхностных слоях заготовки. Эти остаточные напряжения могут привести к увеличению срока службы заготовки, особенно при использовании процесса многопроходного или глубокого шлифования. Исследования показали, что на глубине от 50 до 10 микрон остаточные напряжения в стали 20Х13 могут менять свой знак со сжимающих на растягивающие, что способствует повышению долговечности этого типа стали.
Однако дополнительный чистовой проход может значительно (в 1,5-2 раза) снизить растягивающее напряжение в поверхностном слое. Процесс глубокого шлифования абразивными лентами отличается от многопроходного процесса распределением максимальных контактных температур в зоне резания. Температура обрабатываемой поверхности, в зависимости от условий охлаждения, составляет от 25% до 60% от максимальной температуры.
Температурные дефекты, которые могут возникнуть при обработке в жестких условиях резания, могут быть легко устранены с помощью мягкого хода в процессе зачистки. Также было установлено, что в результате глубокого шлифования абразивными лентами поверхностные слои заготовок из стали 20Х13 и 12Х18Н10Т упрочнялись в 2-3 раза по сравнению с их первоначальной структурой. В то же время поверхностные слои термообработанного сплава D1h были размягчены на глубину 50-100 мкм на 30-45%. Для первых двух материалов твердость и толщина упрочненного слоя уменьшались по мере уменьшения скорости подачи заготовки и глубины резания. Однако для сплава D1ch увеличение скорости подачи и уменьшение глубины резания привели к уменьшению размягчения и глубины размягченного слоя.
Результаты исследований показали, что чистовой ход с глубиной резания, равной глубине дефектного слоя, позволил избежать изменения микротвердости поверхности. Влияние параметров резания на шероховатость поверхности при ленточном шлифовании было аналогичным другим абразивным процессам. Увеличение скорости подачи заготовки, глубины резания и скорости вращения инструмента привело к повышению шероховатости поверхности, в то время как увеличение скорости перемещения инструмента уменьшило шероховатость.
Исходя из вышеизложенного, можно сделать вывод, что ленточное шлифование может помочь создать желаемую картину технологических напряжений в поверхностных слоях деталей. Это может помочь предотвратить появление дефектов поверхности и обеспечить желаемый уровень шероховатости поверхности. Это достигается за счет сочетания черновой и чистовой обработки, а также регулировки параметров обработки. Таким образом, LGSH подходит для использования при производстве и восстановлении различных автомобильных компонентов.
Комментарии 0