Повышение производительности: новейшие методы раскроя листовых сталей
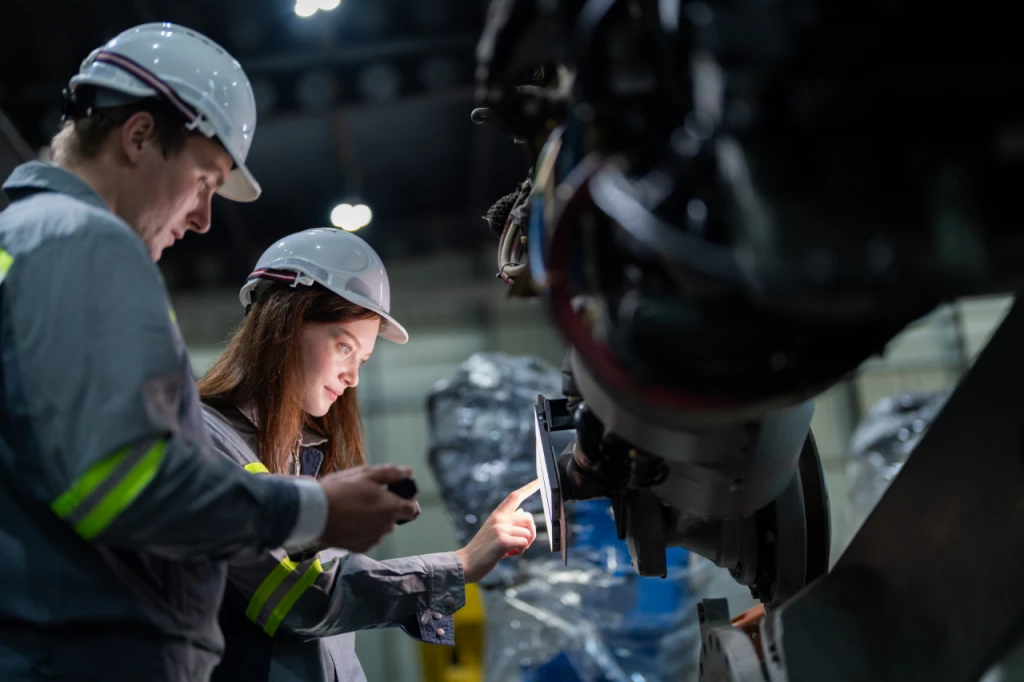
Производственные предприятия, работающие с листовыми сталями, постоянно стремятся к повышению эффективности своих процессов. Одним из ключевых аспектов в этом вопросе является точный и оптимизированный раскрой материала. Новейшие методы раскроя листовых сталей позволяют значительно сократить отходы материала, улучшить качество продукции и увеличить производительность предприятия.
В этой статье мы сравним существующие в наши дни методы обработки листовых материалов в рамках мелкосерийного производства.
Как правило, при мелкосерийном производстве для обработки деталей применяются металлорежущие станки, но из-за использования подобного оборудования больше половины веса металла уходит в стружку, из-за чего стоимость детали увеличивается, так как потеря части веса металла порождает необходимость осуществить дополнительные затраты.
В наши дни альтернативой выступают электрофизические методы, состоящие из лазерной, плазменной, а также гидроабразивной резки. В наши дни данные методы активно набирают популярность, поскольку они не требуют осуществление дальнейшей механической обработки металла, что в значительной степени сокращает количество отходов и стоимость осуществления производственной процессов.
Подобные методы обработки также имеют ряд других важных преимуществ:
благодаря лазерной резке появляется возможность создавать фигуры сложной формы из металла;
благодаря гидроабразивной резке возможно обрабатывать металлы различной плотности и твёрдости;
за счёт плазменной резки появилась возможность проводить обработку даже металлов большой толщины.
Таким образом, внедрение электрофизических методов обработки металла в машиностроении позволяет уменьшить стоимость осуществления производственных процессов без ущерба для качества производимой продукции.
Лазерная резка
Лазерная резка – это процесс раскройки металла, при котором используется лазер. При этом мощность луча может варьироваться в зависимости от выбранного оборудования. Под воздействием лазера металл нагревается и плавится, благодаря чему происходит разделение металла на несколько частей желаемой формы.
Технология лазерной резки применяется во многих сферах жизни человека, поскольку она позволяет осуществить быструю и точную резку материала на части желаемой формы и размера, при этом благодаря лазерной резке появляется возможность создавать детали даже самой сложной формы. Например, подобные технологии широко применяются в медицине, науке и даже в искусстве, поскольку лазерная резка может применяться не только для металла, но и для пластика, стекла, керамики и многих других материалов.
Лазерная резка отличается высокой точностью и минимальным количеством отходов после осуществления производственного процесса. Более того, она может быть автоматизирована, что позволяет не только ускорить процесс производства, но и повысить качество выпускаемой продукции.
Благодаря лазерной резке создаются различные приборы, например, микрочипы и многое другое. Более того, используя подобные технологии, можно за очень короткий период времени создать микросхемы, которые будут отличаться высокой точностью, что положительно скажется на работе электронных устройств, в которые они будут внедрены.
Если говорить об искусстве, то лазер может помочь в создании необычных форм для скульптур. Также лазерные технологии могут помочь в гравировке на стекле, различных металлах и других материалах.
Несмотря на огромное количество достоинств, лазерная резка имеет определённый недостатки. Например, данный метод может быть слишком дорогим для мелкосерийных производств, которые не ставят перед собой цель выпуска большого количество различной продукции. Но при этом лазерная резка всё равно остаётся одни из самых эффективных способов резки металла, так как именно эта технология позволяет осуществить производственные процессы с минимальным количество отходов, что позволяет снизить себестоимость производимой продукции.
Существуют следующие процессы лазерной резки: сублимация, резка плавлением и газокислородная резка. В процессе сублимации металл в зоне разреза испаряется под действием излучения. Благодаря сублимации появляется возможность уменьшить ширину прорези.
Осуществление лазерной резки путём плавления применяется, как правило, для цветных металлов и легированных металлов. В ходе данного процесса происходит плавление материала в зоне разреза, после чего расплавленные участки удаляются благодаря инертному газу. Данный способ позволяет не только ускорить процесс резки металлов, но и предотвратить возникновение различных дефектов в процессе работы.
Лазерную обработку металла путём плавления не следует применять для резки меди или титана, поскольку медь отражает лазер, из-за чего процесс обработки данного металла затрудняется. На титане, в свою очередь, при подобном способе обработки на кромках образуются нитриды и оксиды, которые необходимо удалять.
Несомненно, лазерная резка, осуществляемая путём плавления, является эффективным способом обработки металла, поскольку он позволяет осуществлять резку быстро и качественно. Но не следует забывать об особенностях некоторых металлов, таких как медь и титан, ведь для них подобный способ обработки не подойдёт.
Другим способом обработки металла является газокислородная резка, которая широко применяется в производстве автомобилей, строительстве и других отраслях. При данном способе резки применяется кислород, при помощи которого расплавленный материал удаляется из зоны разреза. Эта технология прекрасно подходит для резки металлов большой толщины без потери скорости работы. Но, стоит понимать, что кромка разреза при данном способе будет получаться далеко не самой качественной, из-за чего возникает необходимость в её доработке.
Не для кого не секрет, что качество конечного результата напрямую зависит от используемого металла и его толщины, а также от давления применяемого при резке газа.
Именно поэтому наиболее целесообразно использовать для лазерной резки те листы металла, которые специально были изготовлены для дальнейшего осуществления лазерной резки, поскольку именно они предполагают хорошее качество поверхности листа, благодаря чему нет необходимости в дальнейшей доработке полученных деталей.
Благодаря лазерной резке вы можете получить невероятно точно вырезанные детали практически из любого материала, поскольку данный метод не воздействует на металл механически, за счёт чего он пригоден даже для очень хрупких металлов.
Применение лазерной резки также возможно в случае с твёрдыми сплавами, поскольку применение данной технологии позволяет обеспечить наиболее точный разрез и качественные края кромки без дефектов, которые могут негативно сказаться на качестве выполненной детали. Даже при условии высокой точности разреза и возможности вырезать невероятно сложные формы, лазерное оборудование имеет достаточно простое управление, что позволяет быстро обучить сотрудников работе с ним.
Но даже при наличии огромного количества достоинств лазерная резка имеет некоторые недостатки:
лазерная река неэффективна в случае с металлами, которые способны отражать лазерный луч (например, в случае с медью);
лазерная резка не подойдёт для обработки металлов слишком большой толщины;
в рамках применения технологии лазерной резки существуют ограничения по габаритам обрабатываемого металла;
скорость обработки детали путём лазерной резки зависит от большого количества различных параметров;
высокая стоимость оборудования для лазерной резки.
Таким образом, лазерная резка является эффективным, но не универсальным способом обработки металла, поскольку для некоторых металлов и сплавов подобная резка не подойдёт. Но, стоит признать, что лазерная резка позволит уменьшить затраты на осуществление производственных процессов без ущерба для качества получаемых деталей.
Плазменная резка
Данный способ резки металла является невероятно эффективным, поэтому он широко используется в различных отраслях промышленности. Этот вид резки функционирует на основе плазмы, которая получается вследствие ионизации газа в высокочастотном электрическом поле. При осуществлении резки плазменная дуга, получившаяся в результате описанного выше процесса, выступает в роли инструмента, непосредственно осуществляющего разрез.
Плазменная резка имеет большое количество преимуществ, среди которых:
возможность обрабатывать металлы большой толщины;
образующаяся плазменная дуга имеет очень высокую температуру, поэтому при помощи плазменной резки можно обработать даже те металлы, которые невозможно разрезать другими способами;
может применяться для большого количества разнообразных металлов, среди которых даже медь и титан, которые не получится качественно обработать, применяя лазерную резку;
позволяет снизить затраты на производственные процессы, поскольку использование подобного способа помогает минимизировать количество отходов и уменьшить время осуществления работы.
Но даже при наличии большого количества преимуществ данный способ имеет свои недостатки:
плазменная резка сопровождается шумом, который может спровоцировать появление проблем со слухом;
в процессе плазменной резки могут появляться опасные для организма вещества.
Разумеется, плазменная резка является невероятно эффективным способом обработки металла, поскольку подобная технология позволяет осуществлять резку металлов, имеющих большую толщину. Но всё же следует понимать, что, используя данный метод, следует соблюдать технику безопасности.
Плазменная резка металла осуществляется при очень высокой температуре, за счёт чего данный способ подходит практически для любых металлов и сплавов.
Плазменная резка бывает:
воздушно-плазменная;
газо-плазменная;
лазерно-плазменная.
Разумеется, данные разновидности плазменной резки имеют определённые сходства, а отличаются они только тем, что при воздушно-плазменной резке используется кислород, а при газо-плазменной - водяной пар.
Для эффективного осуществления плазменной резки плазмообразующие среды должны осуществлять следующие функции:
создание дуги, которая будет обеспечивать резку металла;
создание качественного среза при помощи газа;
обеспечение передачи тепловой энергии металлу.
Стоит отметить, что для обеспечения долговечности оборудования, следует использовать тот газ, который не будет провоцировать износ элементов устройства. Разумеется, применение газа в промышленности позволяет улучшить качество выпускаемых деталей, а также производительность, но к выбору используемого газа тоже стоит подходить ответственно для того, чтобы он не вредил оборудованию и действительно помогал в процессе производства.
Стоит отметить, что по сравнению с газо-плазменной резкой, в процессе плазменной резки обработка металла происходит намного быстрее. Этот метод позволяет минимизировать риск деформации металла, а также исключает проблемы с баллонами кислорода или газа, поскольку подобные дополнительные приспособления в рамках данной технологии не требуются. Более того, благодаря данному методу появляется возможность уменьшить затраты ресурсов, что поможет удешевить производство и исключить неблагоприятное влияние на окружающую среду.
Но, по сравнению с другими методами, плазменная резка также имеет недостатки, поскольку при использовании кислородного метода обработки металла возможно разрезать металлы с больше толщиной, чем при использовании плазменной резки. Более того, при использовании данной технологии необходимо соблюдать определённый угол отклонения, а при безответственному отношению к нему возможно ухудшение качества изготавливаемой продукции. Следует отметить, что оборудование для плазменной резки также отличается высокой сложностью, из-за чего для работы на нём требуется человек, имеющий высокий уровень образования.
Комментарии 0