Оптимизация температурных процессов на нефтегазовых заводах
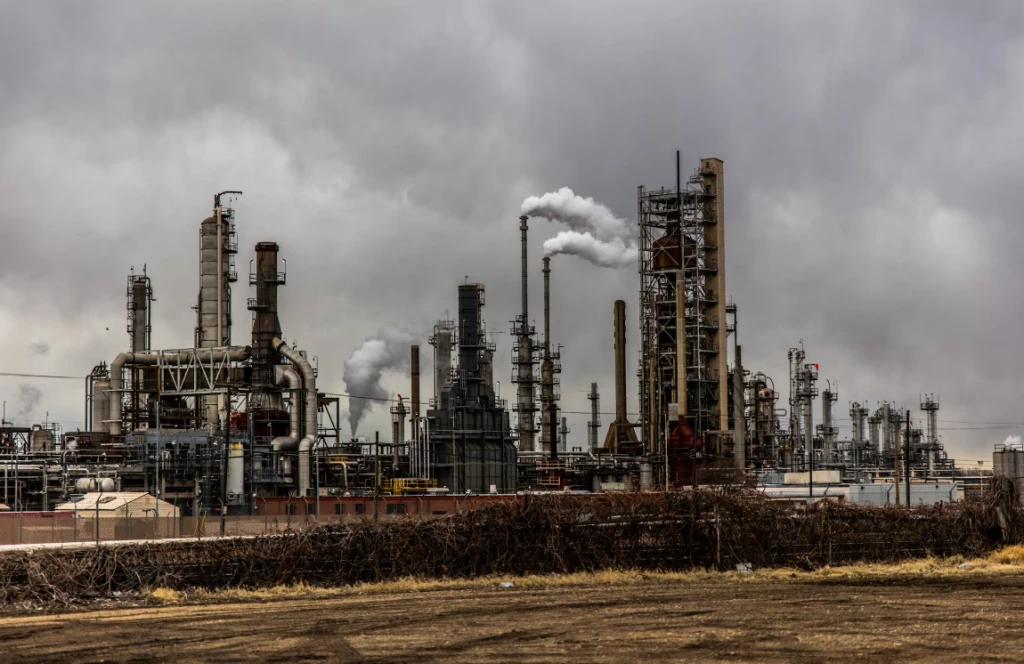
Нефтегазовые заводы являются сложными инженерными сооружениями, где контроль и оптимизация температурных процессов играют важную роль в обеспечении эффективной работы оборудования и производственных процессов. Неправильная температурная регулировка может привести к выходу оборудования из строя, потере продукции и увеличению эксплуатационных расходов. Поэтому нефтегазовые компании постоянно ищут новые инновационные решения для оптимизации температурных процессов на своих заводах.
Избыточное тепло на нефтеперерабатывающих заводах — это упущенная прибыль
Избыточное тепло на нефтеперерабатывающих заводах - это серьезное препятствие для повышения производительности предприятий, особенно во время знойного лета.
Главная проблема заключается в недостаточном охлаждении. Во время лета, когда температура может подниматься до 40 °C, может возникать недостаток охлажденной циркуляционной воды. Это провоцирует повышение температуры пирогаза свыше установленных значений и заставляет понижать производственную мощность. В результате не производится около 2,5 тыс. тонн этилена и 1,5 тыс. тонн пропилена за год с учётом максимальной производительности 435 тыс. тонн.
Ещё один фактор - ускоренная полимеризация в теплообменниках пирогазового тракта межступенчатого охлаждения.
В итоге жаркая погода оказывает негативное влияние на работу и производительность технологических установок. Производительность уменьшается или же её приходится специально уменьшать. Очевидно, что подобная ситуация неприемлема для бизнеса. Как можно добиться хорошего контроля температурного фона на рынке?
Борьба с избыточным теплом: градирни и чиллеры
Проблему избыточного тепла можно решить применяя градирены и чиллеры. В первом образце основа работы состоит в том, чтобы отдать тепло окружающему воздуху. Чиллеры – это особые кондиционеры, использующиеся в промышленности. Необходимые изменения можно достичь, поглотив тепло пока хладон испаряется.
Градирни подразделяются на мокрые и сухие. Если они мокрые, то наблюдается испарение воды в воздухе; если сухие, то вода циркулирует в закрытом контуре. Охлаждение обеспечивают теплообменники.
У любого из данных вариантов есть свои преимущества и недостатки. Модели, имеющие открытый контур, предназначены для больших объектов промышленности, которым нужно охлаждать весомые объёмы воды, таких как нефтеперерабатывающие и нефтехимические предприятия.
К их сильным сторонам можно отнести надёжную работу в условиях жаркой погоды и высокие показатели производительности охлаждения на единицу продукции. Однако наблюдаются и недостатки, включая высокие цены на оборудование и проведение монтажных работ, а также немалые издержки эксплуатации (включая значительный расход воды).
Помимо указанных проблем, также важно учитывать возможность образования коррозии на трубопроводах и развитие вредных микроорганизмов.
У сухих градирней, или "драйкулеров", нет подобных недостатков. Но у них есть свои изъяны, такие как меньшая эффективность по сравнению с мокрыми градирнями и отсутствие возможности понижения температуры технологической воды до определенного уровня без заблаговременного адиабатического охлаждения.
Выбор между градирнями и чиллерами зависит от температурных условий. При температуре от 25 до 35 °C допустимо использование обоих вариантов. Однако в случае превышения 40 °C эффективнее будут градирни, будь то мокрые или сухие. Не забывайте, что летний зной является основным негативным фактором в работе нефтеперерабатывающего завода.
Возможные решения возникающих проблем
Проблемы доступности оборудования для контроля температуры в связи с введёнными санкциями и уходом западных компаний с рынка РФ вызывают ряд опасений.
И всё же не стоит унывать. Российские производители могут предложить альтернативы. Стационарные решения, такие как градирни и чиллеры, медленны и требуют значительных инвестиций.
На производствах необходимо эффективно решать все возникающие вопросы. Однако увеличение скорости процессов не всегда возможно, тут могут быть свои преграды. Если же Вы всё-таки заинтересованы в более дешёвом решении, есть смысл рассмотреть возможность аренды оборудования. Но выгода отнюдь не всегда очевидна.
Увеличение эффективности с помощью пинч-анализа
Для повышения эффективности можно использовать метод пинч-анализа, который поможет оптимизировать потребление энергии в системах теплообмена. Это позволит снизить расходы на охлаждение и повысить производительность предприятия.
В летний период часто возникают проблемы с водоснабжением, особенно в нефтехимической отрасли. Многие предприятия занимаются настройкой и очисткой оборудования для теплообмена. Однако это лишь исправление последствий. Более целесообразно обратить внимание на причину проблемы. Именно недостаточная эффективность рекуперации энергии в системах теплообмена является корнем зла. Чем более эффективно мы это делаем, тем меньше требуется энергии для процесса и соответственно меньше её потребляется. На самом деле есть возможность изменения уровеней энергопотребления, и для этого существуют специальные методы, такие как анализ пинчей.
Анализ пинчей — это методика, направленная на сокращение потребления энергии в химических процессах с помощью расчёта минимально необходимой энергии (или минимума потребления энергии) с учётом термодинамических законов. Применяя данный метод, можно ощутимо сократить расходы за счёт уменьшения использования внешних источников энергии, как для подачи, так и для отвода тепла, путем максимального использования рекуперации тепла, рассматривая данную энерготехническую систему.
Иначе говоря, происходит обмен тепла между горячими и холодными потоками. Это приводит к значительному снижению энергопотребления, особенно летом, когда практически не требуется дополнительного охлаждения. После внедрения интеграции около 80% воздушных и водяных холодильных установок можно вывести из эксплуатации как ненужные.
По мнению ученого, эффективность анализа пинчей в нефтехимической отрасли может достигать 40–70% от общего потребления топлива, а время окупаемости проекта составляет от 6 до 12 месяцев. Однако данные цифры могут варьироваться, завися от возраста предприятия. Наиболее заметный эффект можно достичь на заводах, которые были построены в период советского союза.
Пинч-метод, хоть и не является новым, был придуман в 1977 году. Почему же этот метод всё ещё не получил широкого распространения на нефтеперерабатывающих заводах? Возможно, не считая консерватизма отрасли, существуют объективные причины, которые мешают его внедрению на предприятиях в отрасли нефтепереработки.
Проблемы с теплопотерями возникают из-за высоких температур летом, что приводит к серьезным убыткам на нефтеперерабатывающих и нефтехимических заводах. К примеру, из-за этого было потеряно около 2,5 тыс. тонн этилена и 1,5 тыс. тонн пропилена в год до того, как были проведены мероприятия, направленные на повышение эффективности энергии.
При реализации проектов по энергосбережению возникают сложности и побочные эффекты. Организация межпоточного теплообмена делает все оборудование и процессы взаимосвязанными, что затрудняет пуск оборудования или его переключение на другие режимы.
Также возможны проблемы с неравенством тепловых балансов аппаратов из-за больших расстояний между ними, что требует специальных конструктивно-технологических решений, таких как теплообменники и дополнительные ходы.
Несмотря на возможные трудности, пинч-анализ считается эффективным и относительно дешёвым методом энергосбережения для нефтеперерабатывающего завода. Возможно, в ближайшие годы этот метод получит большее внимание от предприятий нефтепереработки, так как вопросы повышения эффективности становятся все более актуальными.