Композитные материалы – инновация, дающая огромные косвенные экономические эффекты
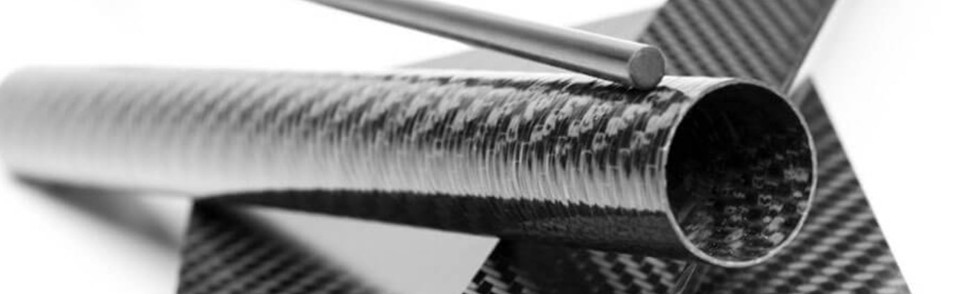
Термин «композиты» вошел в обиход несколько десятилетий назад. Им обозначают неоднородные сплошные материалы, состоящие из двух составных частей – армирующего компонента и матрицы, обеспечивающей совместную работу армирующих компонентов.
Однако сами композитные материалы существуют уже миллионы лет в живой природе. Например, птичьи гнезда, которые сделаны из веток, склеенных глиной.
В антропогенной среде самый распространенный композит – железобетон, сочетающий железную арматуру и бетон. Бетон плохо работает на растяжение и изгиб, но хорошо – на сжатие. Арматура хорошо работает на растяжение и изгиб, их соединяют и получают материал, который включает лучшие свойства двух различных материалов.
Главным двигателем эволюции композитов всегда была авиация, потому что она предъявляет наибольшие требования к материалам. Два ярких примера:
Дельта-древесина (ДСП-10, балинит), созданная в ВИАМе (Всесоюзном научно-исследовательском институте авиационных материалов) в начале 1940-х, была одним из секретов нашей Победы. Дело в том, что в СССР того времени не было материалов для поточного производства самолетов: ни технологичных металлов (алюминиевых сплавов и высоколегированных сталей), ни древесины для цельнодеревянных конструкций (отечественные породы деревьев не подходили для авиации). Тогда наши ученые и придумали склеить шпон карельской березы фенолформальдегидными смолами (бакелитовым лаком), а потом подвергнуть его горячему прессованию под высоким давлением. Получившийся композит, который еще называют авиационной фанерой, плохо горел и не уступал по прочности алюминию. Этот материал и сейчас можно купить в магазинах. Его используют в строительстве и производстве мебели.
Плитка теплозащитного покрытия для корабля «Буран», созданная в том же ВИАМе из материала на основе особо чистых кварцевых волокон, сейчас используется в пекарнях и на хлебозаводах. Эта плитка выдерживает температуру свыше 1500 градусов, но сама почти не нагревается: через минуту после изъятия из печи ее спокойно можно брать голыми руками.
Раз композиты существуют уже многие десятки лет, почему их всё равно можно считать инновацией? Потому что сейчас под новые задачи постоянно разрабатываются новые композиты. Более того, материаловеды, используя разные исходные компоненты, разные режимы совмещения, разные отвердители, научились создавать композиты с необходимыми индивидуальными свойствами. Это есть основное ноу-хау.
Если сравнить металлы и композиты, то по любому физическому свойству (твердость, прочность, мягкость, теплопроводность и т. д.) в 99 % случаев композиты будут лучше. Именно поэтому композиты продолжат теснить металлы и другие широко распространенные материалы.
Особенности композитных материалов
Как композитам удалось опередить металлы по физическим характеристикам? Просто свойства композита превосходят свойства его составных элементов. Представьте себе прутик. Сломать его проще простого. Но если много прутиков связать в веник, то сломать его практически невозможно.
Другие ключевые особенности композитных материалов:
два и более компонента;
новые уникальные свойства, отличные от свойств его составных частей;
неоднородность в микромасштабе и однородность в макромасштабе;
состав, форма и распределение компонентов заданы заранее.
Также композитам присуща анизотропия свойств – в разных направлениях эти материалы могут иметь разную прочность, жесткость и т. д. Умелые инженеры и конструкторы успешно используют эту особенность.
Где применяют композитные материалы
Двух- и более компонентные материалы всё шире применяются в авиа- и судостроении. Для конвейерного производства автомобилей они еще слишком дороги, поэтому пока композиты стали неотъемлемой частью гоночных болидов и машин премиум-класса. Композитный кузов автомобиля существенно легче металлического, что позволяет улучшить маневренность и уменьшить расход топлива.
В число других сфер, где все чаще используются композиты, входят:
энергетика. Из композитов делают ребра жесткости ветролопастей, которые могут достигать длины 90 метров. Сейчас ученые работают над созданием композитных материалов, которые помогут улучшить эффективность турбин за счет увеличения их рабочей температуры;
строительство. Углепластиковыми композитами армируют дорожное полотно. Это увеличивает срок его эксплуатации на несколько лет. Мост в селе Языково Ульяновской области через реку Соловей, созданный с применением композитов, рассчитан на нагрузку до 100 000 кг, то есть по нему спокойно может проехать комплекс «Тополь-М» (80 тонн). Система внешнего армирования композитами способна восстановить несущую способность конструктивных элементов зданий. Причем такой ремонт можно произвести в короткие сроки без длительной приостановки эксплуатации объекта;
медицина. Кристаллическая решетка углепластика биологически инертна, так что иммунитет не распознает ее как нечто чужеродное и ткани спокойно в нее прорастают. Поэтому из композитов делают искусственные суставы, кости и зубы. В ЮФУ сейчас разрабатывают композит для создания роговицы;
добыча полезных ископаемых. Обычные износостойкие ролики для горно-обогатительных комбинатов служат 1 год, а композитные – не менее 5 лет. Таков срок гарантии производителя на это изделие.
Также композиты применяются в производстве бытовой техники и спортивного инвентаря. И число сфер их применения будет только расти.
Композитные материалы в России
Рынок композитов в России растет в среднем на 10–15 % в год, успешно развиваясь благодаря научным открытиям. Поэтому его можно считать одним из самых перспективных в нашей стране, что понимают и в Правительстве.
В конце января 2021 года Михаил Мишустин распорядился основать в Тульской области инновационный научно-технологический центр «Композитная долина», где будет организован полный цикл создания высокотехнологичной продукции – от науки до действующего производства.
Вообще, в середине прошлого века наша страна была лидером «композитной гонки». В Советском Союзе раньше, чем в Японии создали высокопрочные углеродные волокна на основе полиакрилонитрильных (ПАН) волокон, из которых сейчас изготавливают многие композитные материалы.
Однако в СССР композиты массово использовались лишь в оборонке и в космической отрасли, а на гражданке их не было. Итог – разрушение отрасли, которая, к счастью, сейчас возрождается, поскольку производство и широкое применение композитов, кроме понятного прямого экономического эффекта, дает массу косвенных. Простые примеры из недавнего прошлого:
в свое время самолет Ан-124 «Руслан» был лидером по числу деталей, созданных из композитов (5500 кг). Это облегчило крылатую машину настолько, что за годы ее эксплуатации удалось сэкономить 18 тыс. тонн топлива;
композиты в конструкции ракеты-носителя «Протон» обеспечили экономию в $2,5 млн при каждом пуске;
использование отечественных стеклопластиковых труб на северокавказских нефтяных месторождениях не менее чем в 10 раз уменьшило количество порывов трубопроводов.
Ближайшее будущее остается за композитами еще и потому, что, во-первых, традиционные материалы давно приблизились к пределу своих физических возможностей, а во-вторых, композиты будут дешеветь, а значит, их можно будет применять при производстве все большего количества товаров народного потребления. Так что те страны, которые организуют полный цикл их производства, получат серьезное конкурентное преимущество.
А вот в средне- и долгосрочной перспективе на передний план, возможно, выйдут интеллектуальные материалы, которые смогут меняться, подстраиваясь под условия окружающей среды. Они будут иметь некое подобие нервной системы. И самолет уподобится живому существу и, как птица, никогда не уйдет в штопор.
Комментарии 0