Дуговая наплавка: современные технологии и преимущества
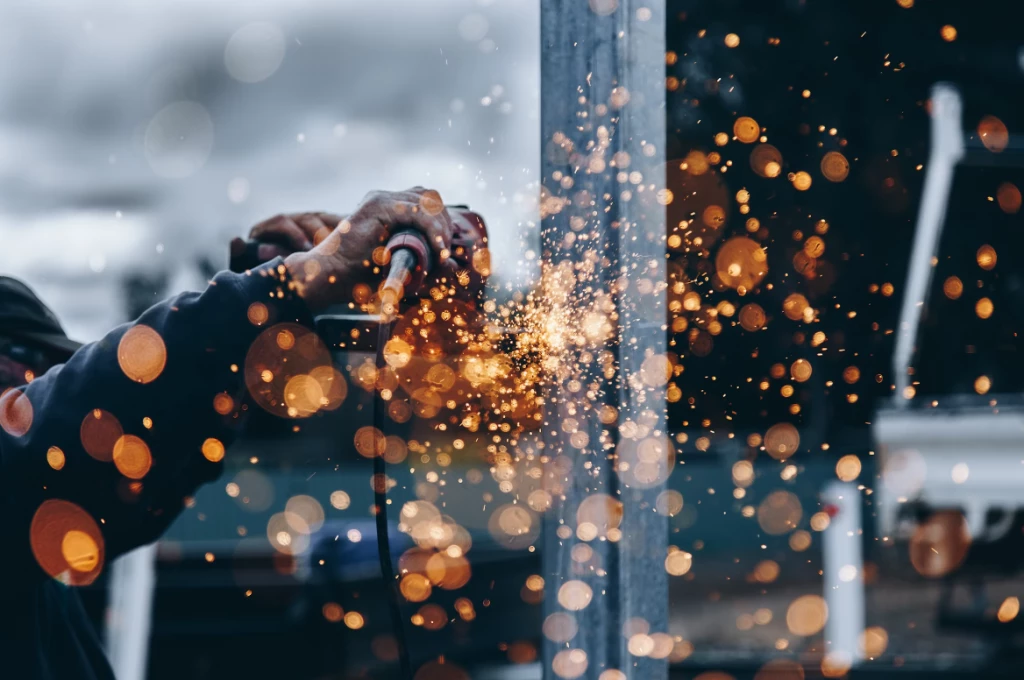
Дуговая наплавка – это один из наиболее распространенных способов соединения металлов, который широко используется в различных отраслях промышленности, от машиностроения до судостроения и аэрокосмической промышленности. За счет своей высокой эффективности, надежности и гибкости дуговая наплавка остается одним из самых популярных методов сварки.
Технологические аспекты наплавки
Можно сваривать металл, который имеет состав, структуру и свойства, сходные с основным металлом, или может существенно отличаться от него. В последнем случае перед сваркой на основной металл часто наносятся промежуточные слои. Во время наплавки крайне важно ограничить смешивание наносимого металла с основным металлом, чтобы обеспечить желаемый химический состав наносимого слоя и предотвратить образование трещин. Кроме того, зона термического воздействия во время наплавки должна быть сведена к минимуму, чтобы избежать значительных сварочных напряжений и деформаций.
Преимущества дуговой наплавки
Высокая прочность шва: дуговая наплавка позволяет достичь высокой прочности шва, что обеспечивает надежность и долговечность изделия.
Высокая точность: современные технологии дуговой наплавки обеспечивают высокую точность и повторяемость процесса, что позволяет достичь высокой точности шва.
Уменьшение деформации металла: дуговая наплавка позволяет уменьшить деформацию металла, что обеспечивает сохранение его свойств и формы.
Увеличение производительности: автоматизация процесса дуговой наплавки позволяет уменьшить время производства и увеличить производительность.
Уменьшение затрат: дуговая наплавка позволяет уменьшить затраты на материалы и энергию, что обеспечивает экономию средств.
Широкие возможности применения: дуговая наплавка может быть использована для соединения различных металлов и сплавов, что делает ее универсальной технологией.
Подготовка поверхности к наплавке
Перед наплавкой поверхность тщательно очищается от масла, краски, окалины и других загрязнений. Любые дефекты поверхности, включая ранее заклепанные участки, удаляются с помощью механических инструментов или инструментов для кислородной резки поверхности. Для снижения сварочных напряжений и обеспечения равномерной толщины наплавляемого слоя необходима гладкая поверхность. Неровную поверхность с большими перепадами высот можно выровнять механическим способом с помощью металлорежущего оборудования. При подготовке поверхности для наплавки с местным износом важно избегать резких переходов между наплавляемым металлом и основным металлом. Наплавка как плоских, так и фасонных поверхностей может производиться отдельными роликами или челночным методом.
Отдельными валиками каждый валик наносится на всю длину поверхности с зазором между ними, равным одной трети их ширины. После очистки валиков от шлака зазоры между ними заполняются. Также используются другие методы прокатки, такие как наложение следующего ролика внахлест после очистки предыдущего от шлака.
Челночный метод подходит для поверхностей шириной от 40 до 80 сантиметров. Преимущество этого метода в том, что на предыдущем валике не успевает застыть шлак, поэтому его не нужно удалять. Существует три способа обработки поверхностей вращения: по образующим, по кругу или по спирали.
Обработка поверхности по образующим может производиться с помощью отдельных роликов, аналогично тому, как это делается на плоских поверхностях. Во время обработки изделие периодически переворачивают в нижнее положение.
Наплавку по окружности также можно производить отдельными валиками. Следующий валик наносится после очистки предыдущего от шлака с перекрытием примерно на 1/3 ширины валика.
Спиральная наплавка выполняется непрерывно. Для предотвращения деформации можно использовать подпружиненные фрезы для очистки предыдущего валика от шлака. В процессе наплавки в изделии могут возникать внутренние напряжения, которые приводят к деформации, а иногда и к разрушению.
Чтобы предотвратить эти напряжения или уменьшить их влияние на деформацию изделия, можно принять несколько мер:
предварительный нагрев изделия до температуры от 200 до 400 градусов цельсия;
проведение процесса наплавки, когда изделие погружено в воду, при этом необходимо следить за тем, чтобы обрабатываемая поверхность не была влажной;
жесткое закрепление продукта в устройстве во время технологического процесса;
термическая обработка изделия после наплавки путем нагревания его до температуры от 650 до 680 градусов цельсия.
Дуговая наплавка – это современная и эффективная технология, которая широко используется в различных отраслях промышленности. За счет своих преимуществ, таких как высокая производительность, качество, гибкость, экономичность и безопасность, дуговая наплавка остается одним из наиболее популярных методов сварки.